Frequently Asked Questions
Find answers to common questions about our products and services.
All About ATS Duct: FAQs
At ATS Duct, we prioritize clarity and transparency in all of our services and products. Our goal is to provide our customers with comprehensive information to ensure they make well-informed decisions. In this FAQ section, you’ll find answers to some of the most common questions we receive about our fire-safe, corrosion-resistant duct systems.
Whether you’re looking for details about our product offerings, manufacturing processes, or the industries we serve, this section is designed to provide quick, helpful insights. If you have any further questions, don’t hesitate to reach out directly—we’re here to help!
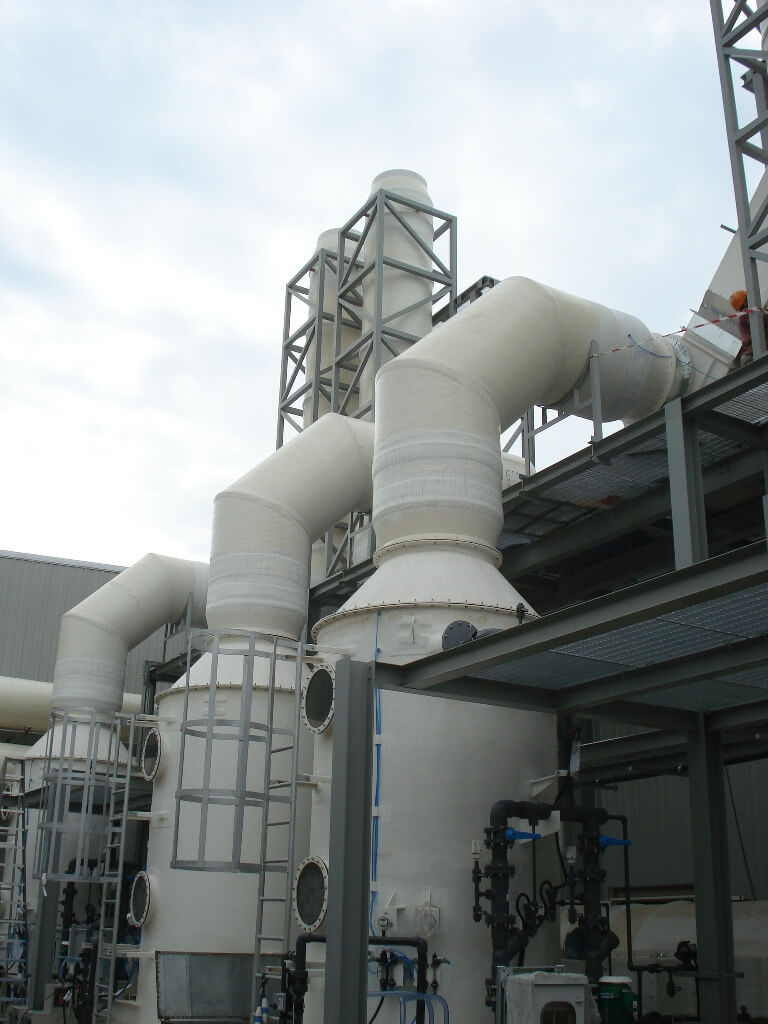
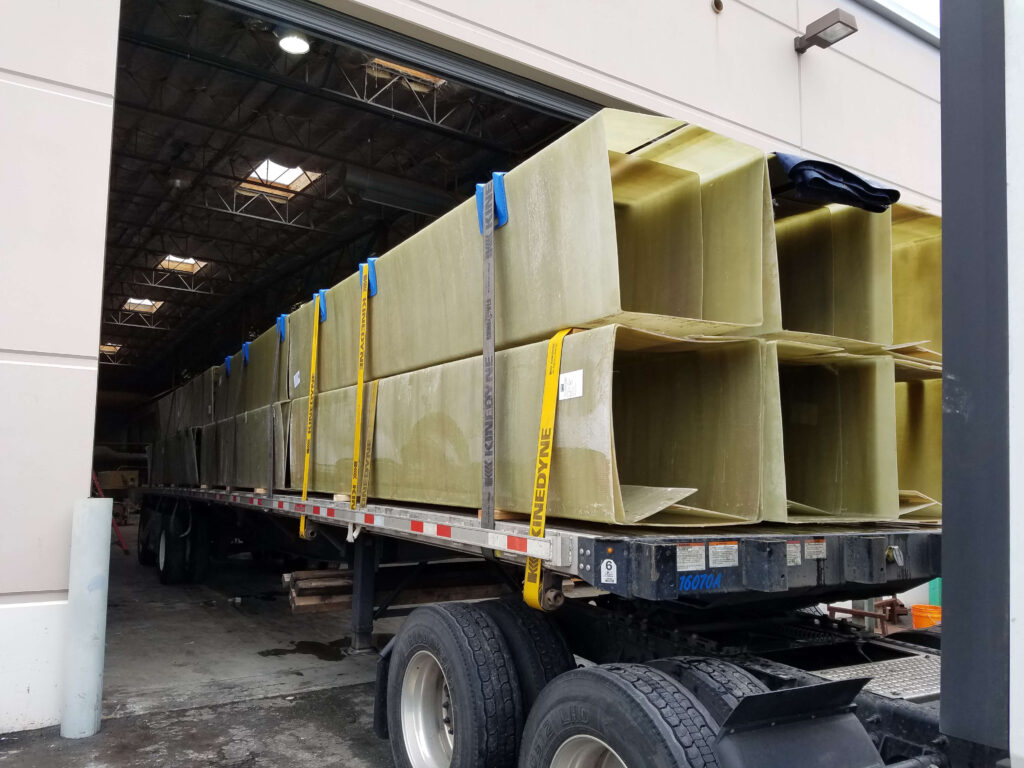
Your Questions Answered
Frequently Asked Questions about ATS Duct
Does ATS have a local representative or factory in my territory?
Representatives: ATS has representatives in the following locations:
– MD of Korea, serving Korea and China.
– TIS of Singapore, serving Southeast Asia.
– ATS in the USA, serving all other locations.
Factories: ATS has factories in several locations. Refer to the maps in the provided documentation for exact locations. ATS also licenses its technology to other companies, which manufacture and sell ducts in various regions globally.
What sizes of duct does ATS make?
ATS manufactures round ducts in sizes from 2ӯ (50 mm) to 160ӯ (4000 mm). ATS also makes rectangular and oval ductwork. Detailed specifications can be found in the Mechanical Drawing Guide, Section 3, pages 45-124.
Who are ATS’ customers?
ATS’ ducts are used in various industries, including:
– Semiconductor
– Silicon and Gallium Arsenide Wafer manufacturing
– Disc Drive/Memory/Storage facilities
– Research & Development
– University Microelectronics
– Pharmaceutical
– Wastewater Treatment
– Paper and Pulp
What are the advantages of ATS FXP™ duct over lined stainless steel?
The advantages of ATS FXP™ duct over lined stainless steel include:
– Flexibility for modifications on-site.
– The ability to make taps on live operating systems using 100%-seal hot taps with internal flanges and 100% seal joints.
What is the thickness of ATS FXP™ duct corrosion-resistant liner?
ATS FXP™ duct liners are a minimum of approximately 100 mils thick, depending on the diameter of the duct. The corrosion resistance is mainly determined by the resin used, which is a high-grade vinyl ester resin applied to the initial liner layer.
What is the difference between a liner and a veil?
A liner forms the corrosion-resistant barrier of the duct, typically made from resin-saturated glass or synthetic veil. The liner’s corrosion resistance is determined by the type of resin used, while the veil offers an additional layer of protection. Synthetic veils are preferable in corrosive environments.
Does a composite duct with a halar veil mean the duct has a halar liner?
No, the presence of a halar veil does not guarantee the duct has a halar liner. The resin used to saturate the veil is the determining factor for the duct’s corrosion resistance.
What happens if a city requires sprinklers in ATS FXP™ duct?
If sprinklers are required, ATS will help assess the validity of this requirement. While ATS FXP™ ducts have superior technical characteristics and approvals, there may be specific circumstances requiring sprinklers. ATS will ensure compliance with local regulations.
How many square feet of manufacturing space does ATS have worldwide?
ATS has a total of 80,000 square feet (8,000 m²) of manufacturing space across two locations: Richmond, California, and Johor, Malaysia, each with 40,000 square feet (4,000 m²).
What is ATS’ manufacturing capacity in linear feet of duct per day?
ATS manufactures 1,500 linear feet of duct per day, with the ability to increase production through extra shifts to meet project deadlines.
Does ATS install duct?
ATS does not provide installation services but works with licensed partners who offer duct installation services worldwide.
How does the cost of ATS compare on an installed basis to lined stainless steel?
The installation cost is similar, but ATS offers cost savings in modularity and flexibility. ATS ducts can be ordered before exact layouts are known, saving on material costs and reducing project timelines.
What is the shelf life of ATS FXP™ duct that has not yet been installed?
ATS FXP™ duct has no shelf life but should be stored properly in dry, clean conditions. Improper handling and storage may compromise the duct’s integrity.
Does ATS offer factory-bonded sections of duct (spooling)?
Yes, ATS offers spooled duct sections upon request. These orders may take longer to process, as they require additional manufacturing steps.
Can ATS provide flanged ducts?
Yes, ATS can provide flanged ducts upon request. Flanges can be supplied with ATS H-Collar™ and ATS Slip Collar™ methods, as well as ATS Van Stone Flanges™ and ATS ISO Flanges™.
How do you connect ATS to regular FRP, PVC, Polypropylene, and lined stainless steel?
ATS ducts can be connected to other materials using flanges, with detailed instructions available for joining dissimilar materials.
Is there a warranty for ATS products?
ATS offers a standard two-year warranty on their products, provided they are installed according to the manufacturer’s recommendations. Extended warranties are available with annual audits.
What is Factory Mutual’s current standard for fire resistance?
ATS FXP™ ducts are FM4922 certified, meeting strict fire resistance standards. These ducts can be installed without internal fire suppression sprinklers, depending on specific use cases.
How do you prevent dust when cutting duct?
ATS recommends using a Vacuum Saw to minimize dust during cutting. For live taps, a two-person team with a jigsaw and vacuum is suggested to ensure proper dust control.
How do you protect the cut edges of the duct?
ATS provides H-Collars and Slip Saddle Taps to automatically protect the cut edges of the duct.
Have More Questions? We’re Here to Help!
Click here to change this text. Lorem ipsum dolor sit amet, consectetur adipiscing elit. Ut elit tellus, luctus nec ullamcorper mattis, pulvinar dapibus leo.