Since 1971, ATS Duct has been the industry leader in fire-safe and corrosion-resistant ducting solutions. Our FM4922-approved FXP™ ducts are engineered to provide unmatched safety, reliability, and compliance for semiconductor fabs, cleanrooms, and industrial exhaust systems worldwide.
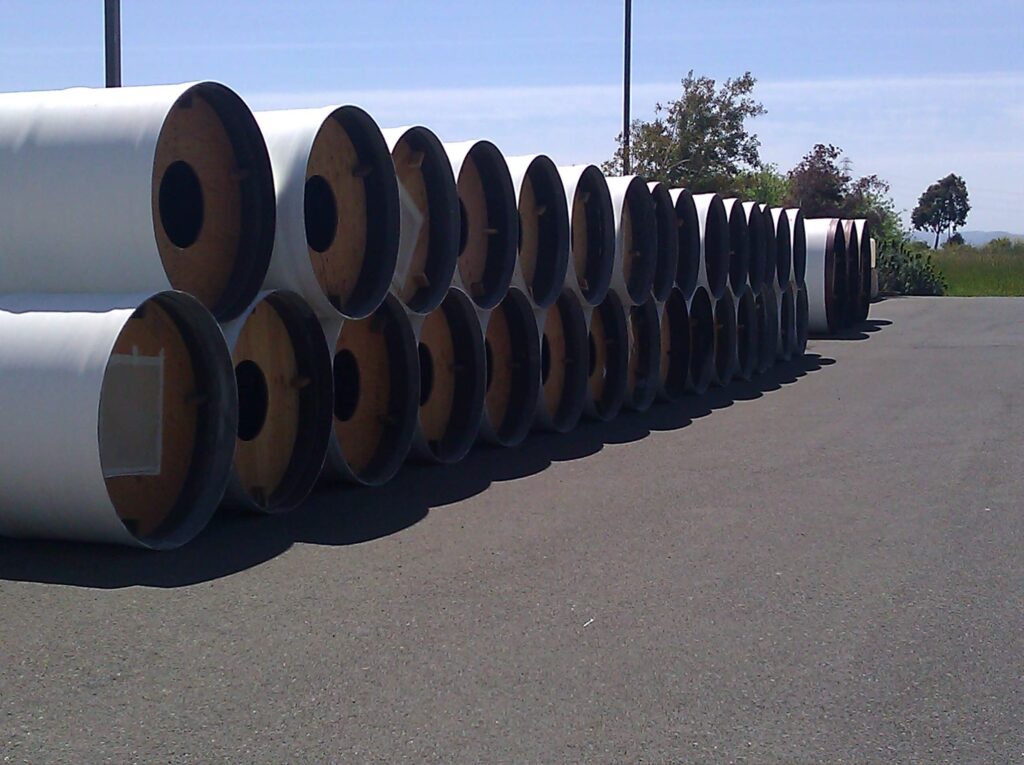
Industry-Leading Fire-Safe & Corrosion-Resistant Ducting
ATS FXP™ ducts provide superior performance in semiconductor fabs, photovoltaic plants, research labs, and industrial environments, ensuring compliance with FM4922, NFPA 318, and ASTM E-136 fire protection standards.
Leak-Proof Connections for Maximum Safety & Efficiency
ATS provides precision-engineered joining solutions to eliminate leaks, reduce VOC emissions, and enhance durability.
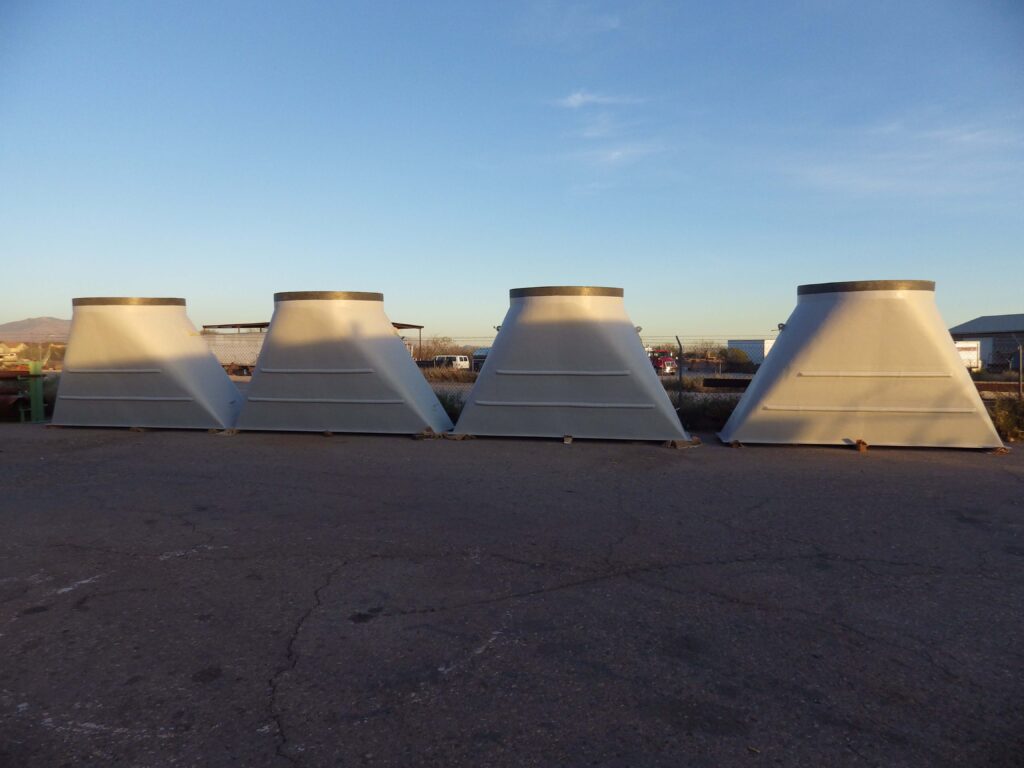
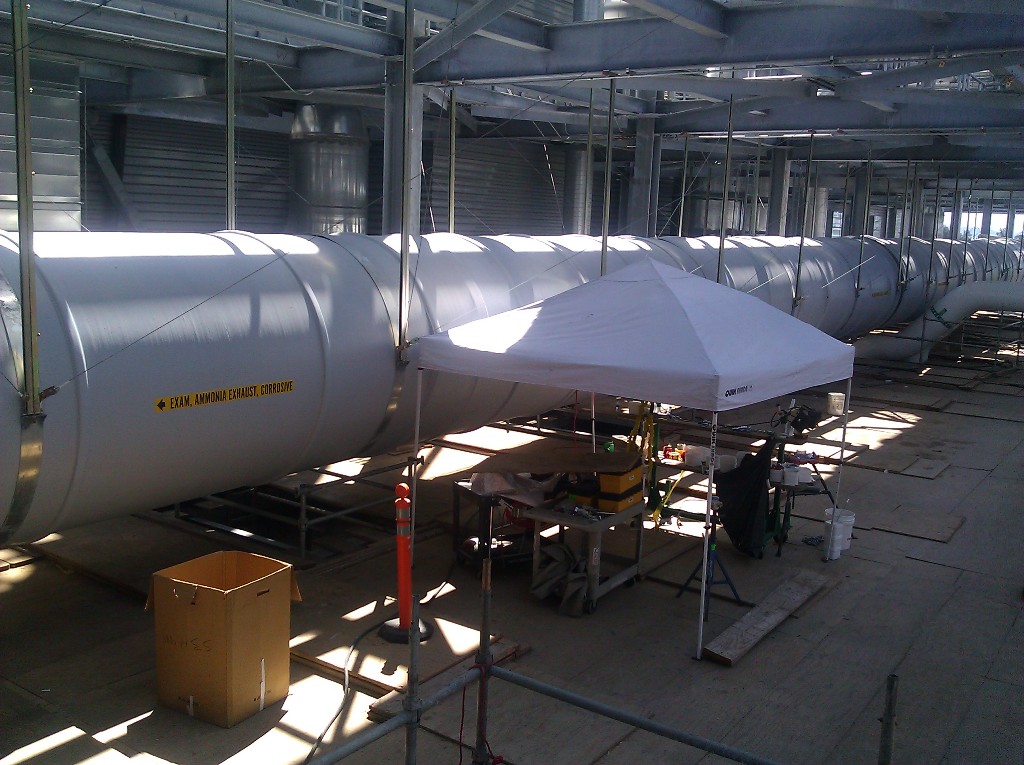
End-to-End Solutions for Seamless Installation & Support
ATS provides complete support for duct system design, installation, and ongoing maintenance, ensuring regulatory compliance and operational efficiency.
Technical Resources
Why Choose ATS Duct?
Ensure the safety and efficiency of your operations with ATS Duct